How IoT Platforms Are Changing the Future of Field Service
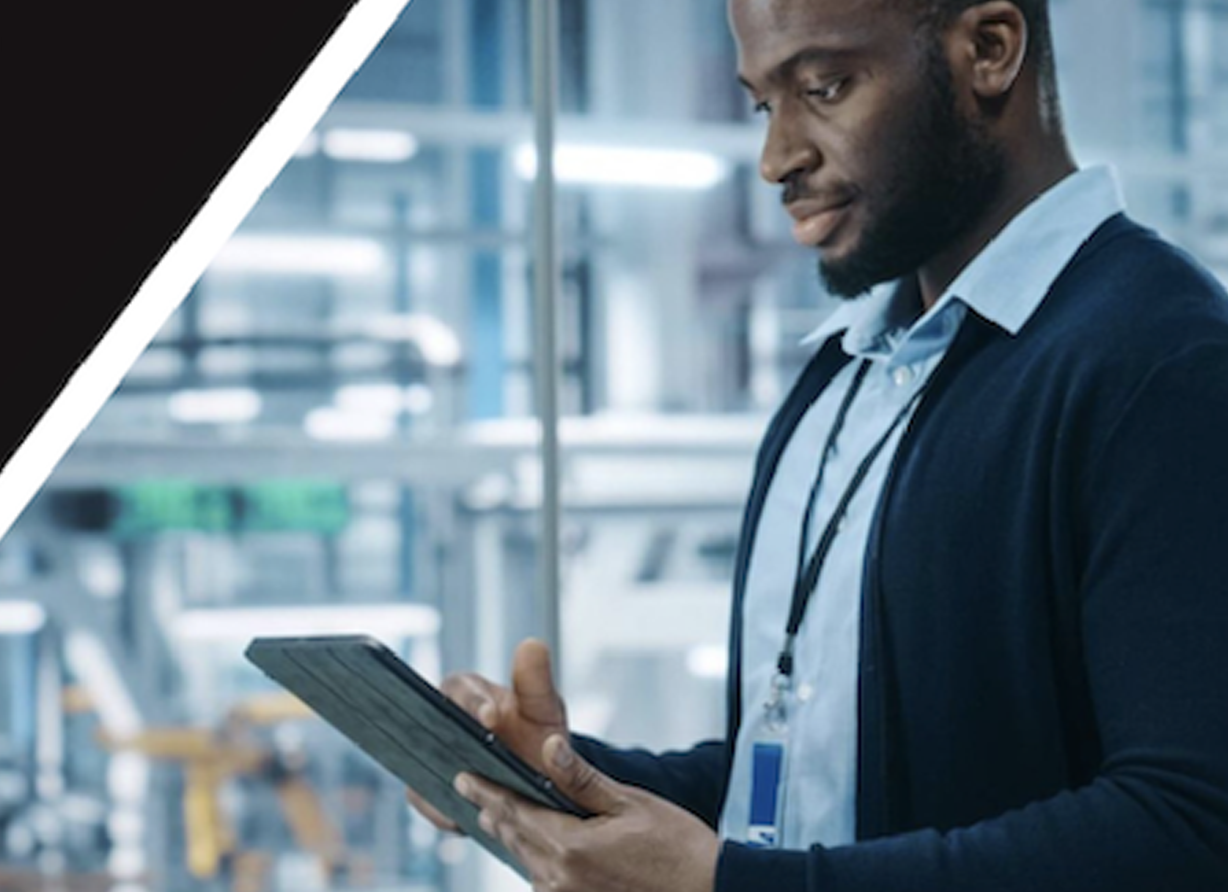
Published Date
It’s no secret that the emergence of the Internet of Things (IoT) has revolutionized the field service industry. In fact, asset tracking and monitoring was one of the largest IoT segments in 2022, seeing a whopping $17.2 billion in revenue. IoT platforms have made it possible to connect devices and equipment on a large scale, enabling real-time tracking and monitoring of performance data. This has led to significant changes in the way field service operations are conducted and managed, as well as how businesses operate overall.
Bolt Data has spent over 10 years working with and understanding the benefits of IoT and harnessing the immense power of its capabilities. This serves to empower companies across industries to reach their highest potential.
Improved Asset Monitoring
Bolt Data Connect provides team leaders like IT Directors, CIOs, Database Engineers, Technology Innovation Managers, and more with real-time actionable data from IoT-connected assets. This data-centric approach with IoT applications delivers the visibility needed to maintain, control, and operationalize asset management. In turn, this enables service teams to reduce costs, eliminate truck rolls, and resolve asset issues remotely.
Bolt Data Connect’s software solution monitors data from IoT devices and uses a predictive algorithm that tracks installed sensors, sends real-time performance data, and enables communication between machines, software solutions, and cloud technology. The predictive algorithm also schedules service resources as needed.
The best part is, Bolt Data Connect’s innovative IoT platform allows service teams to stay ahead of issues before they arise. This results in the extension of asset lifespans, reduced maintenance costs, and increased asset uptime.
Increased Efficiency and Productivity
By increasing efficiency and productivity, service teams avoid the need to dispatch a technician for every asset issue. This allows field service technicians to remotely monitor and diagnose equipment malfunctions, as well as send remote commands to fix asset issues. In fact, Bolt Data’s IoT applications have made it possible to eliminate 30 percent of truck rolls. For a company with 1,000 machines serviced twice each year, this equates to 600 fewer truck rolls and a cost savings of $300,000.
This also benefits technicians who may need to repair an asset in a remote location or are experiencing an internet outage. Long gone are the days of waiting for the internet to boot back up! Bolt Data Connect enables internet connectivity and offline processing to maintain efficiency and productivity.
Your real-time asset data from IoT-connected devices are live-streamed into Bolt Data Connect, which can then be viewed by IT departments and technicians at any time. With this data, it’s easier for your team to suggest actionable items to extend the health and effectiveness of the asset. These customized solutions are entirely data-driven and based on the usage of your specific device, furthering the capabilities of your field service by the utilization of our IoT cloud system.
Enhanced Customer and Service Team Experience with IoT Monitoring of Devices
Bolt Data Connect’s predictive maintenance capabilities reduce the likelihood of asset malfunction and downtime. With Bolt Data Connect’s real-time asset IoT device monitoring capabilities, any anomalies and faults are detected and reported immediately. The Sensor Data Reporting capability also helps technicians quickly determine the events that led up to an asset issue, reducing service and repair times. Not only does this enhance your service team’s experience, but also improves overall business operations.
Less asset downtime and a more optimal allocation of resources mean a better overall experience for team members and customers. On average, about 10-15 percent of the time when an engineer arrives to fix an asset, they report a “No Fault Found.” However, when calls are first routed through a triage phase, this increases first-time fix rates from 62 percent to 86 percent. This helps service teams complete their job, allows assets to be back online faster, and empowers organizations to provide customers with the services they need, when they need them.
Additionally, Bolt Data Connect’s IoT monitoring systems not only enhance asset safety but also ensure compliance with regulatory standards. Because Bolt Data Connect constantly monitors your assets, it can capture data on asset usage, maintenance activities, and asset maintenance history, which can furthermore be used to demonstrate compliance with regulatory requirements. All asset data can be found in the seamlessly integrated Bolt Data IoT cloud software system.
Begin Your IoT Journey To Elevate Your Business Operations
There are myriad benefits of IoT-enabled devices, and IoT platforms have enabled organizations to increase efficiency, productivity, and safety automatically and remotely. See how your business, service teams, and customers can thrive with Bolt Data Connect’s integration of IoT cloud systems and IoT-connected devices.
Bolt Data is leading the field service industry with IoT and digital asset data monitoring solutions to help build remarkable service organizations around the globe. To learn more about how we can unlock the potential of your asset data from IoT-connected devices, contact us today.